Process and quality monitoring
The process monitoring happens during the machining
The system
Due to the integrated measuring and evaluation system the process parameters are analyzed during the machining, what gives the possibility to automatically intervene in the process before the part or tool gets damaged.
The process optimization
Cutting speed and parameter optimization
Cutting oil and tool optimization
Tool life optimization
Cycle time optimization
Process analysis
Profits
No additional monitoring system necessary
Detection of errors and deficiencies
Higher productivity
Shorter cycle times
Reduction of material rejects
Tool protection
Lower tool wear
Process evaluation
Quality assurance
Reduction of costs
Examples: Process deviation and error during the machining.
Monitoring of the maximum torque is always active to protect the tool.
The minimum torque is optional adjustable.
Additional parameters are evaluated in combination with the torque, i.e.: Depth, time, feed orientation etc.
The torque is visualized as arrow around the tapping tool:
green | → | correct torque |
blue | → | torque too low |
red | → | torque too high or error |
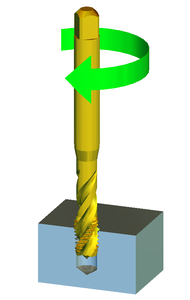
No Error
The thread complies with the
required quality
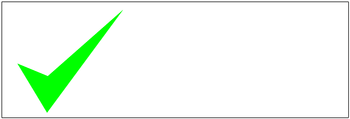
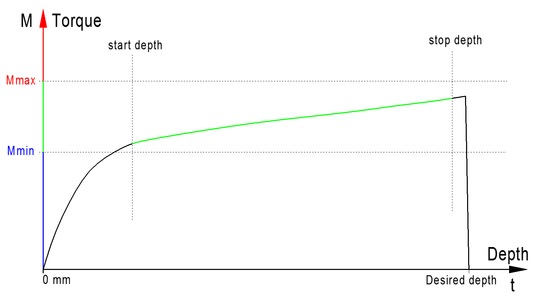
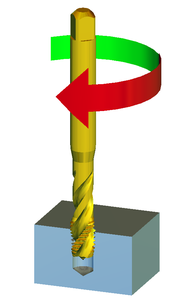
Tool wear
Detection of a worn tool

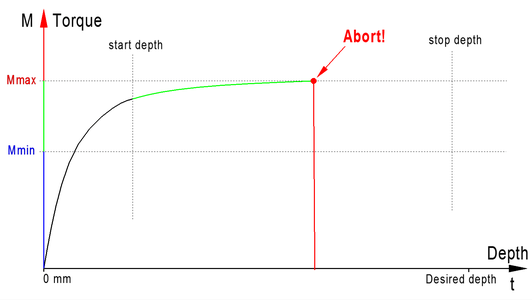
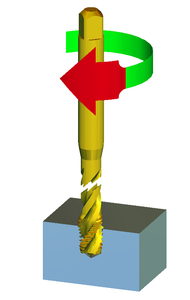
Prevention of tool breakage
due to too low drilling depth
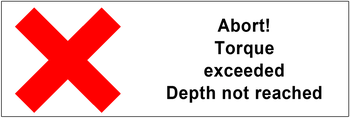

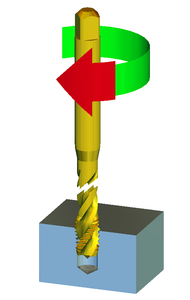
Prevention of tool breakage
due to fatigue
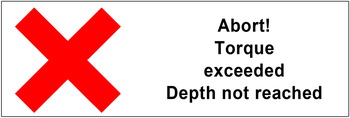
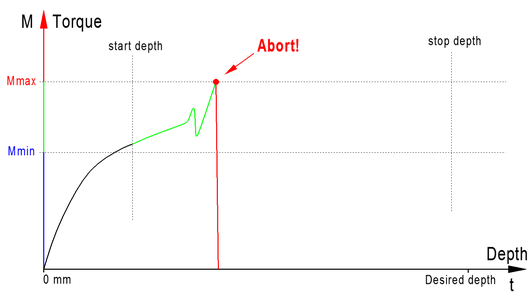
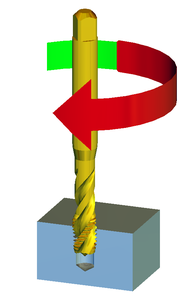
Drilling too small
Detection of a too small drilling
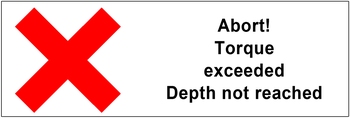
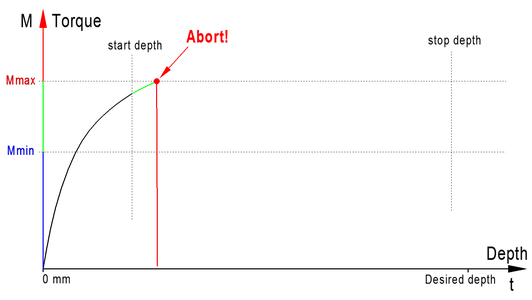
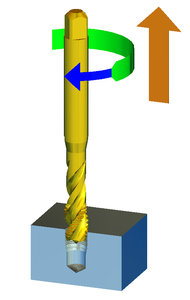
Detection of torn out threads
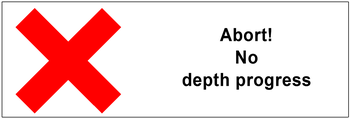
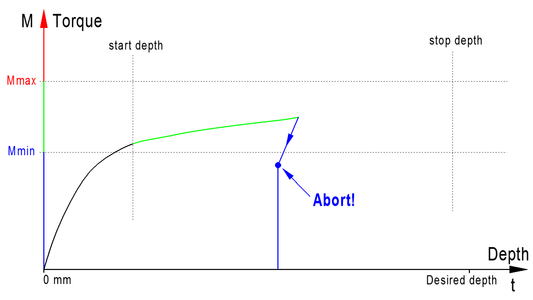
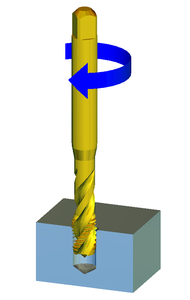
Drilling too large
Detection of a too large tap
drill diameter
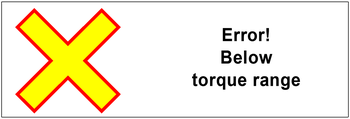
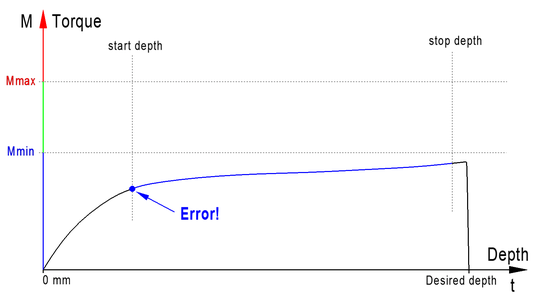
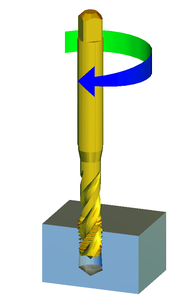
Detection of a conical drilling
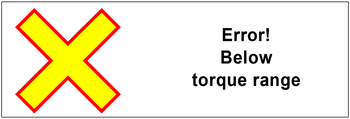

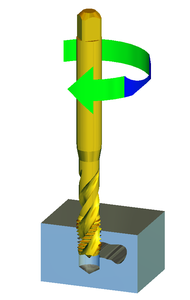
Detection of cavities
(air pockets and blow holes)
within castings
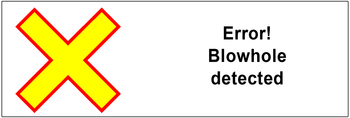
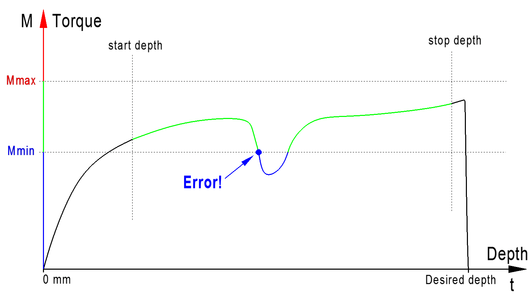

Detection of a missing borehole
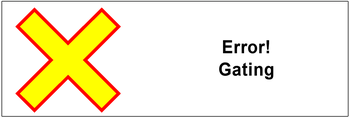
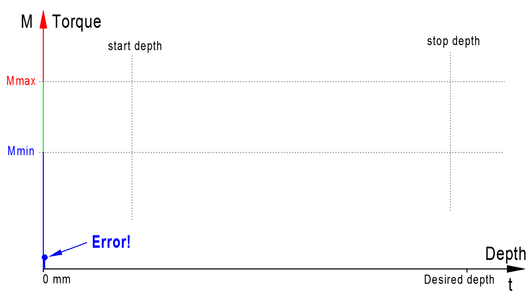
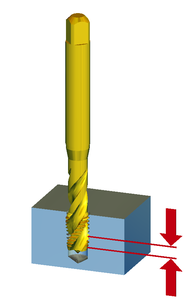
Detection of a differing thread depth

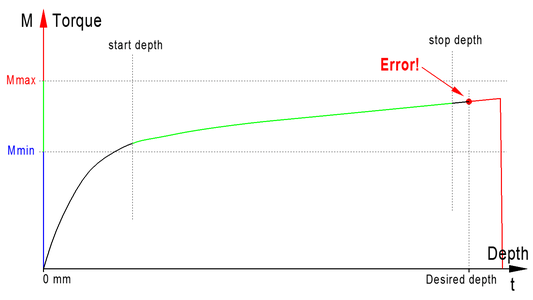