Know-How
Technische Details
Gewindebearbeitung mit Tauro & Taurox
Mithilfe eines Ausgleichssystems wird die Antriebsspindel während der Bearbeitung in einem Schwebezustand gehalten. Dies verhindert die axiale Belastung auf das Gewindewerkzeug, das sich durch seine Geometrie selbst in das zu bearbeitende Werkstück einzieht. Die Eingabe der Gewindesteigung ist nicht mehr notwendig, weil die Tiefe während der Bearbeitung ab dem Werkstücknullpunkt über ein Messsystem permanent überwacht wird. Das Werkzeug findet den Gewindegang immer wieder und macht so auch das Nachbearbeiten von Werkstücken möglich.
Einfache Bedienung
Ein 4,3" TFT-Display mit Drehgeber und Tasten erlaubt eine übersichtliche menügeführte Bedienung der Tauro und Taurox-Maschinen. Zudem ermöglicht es eine einfache Eingabe von Bearbeitungs- und Qualitätsparametern. Verschiedene Werkzeuge lassen sich über ein Schnellwechselsystem bequem einspannen. Je nach Startmodus erkennt die Maschine bei drehender Spindel den Werkstücknullpunkt.
Intelligente Steuerung
Die leistungsstarken Prozessoren der einzelnen Module der Tauro und Taurox-Serie sind über ein Bussystem vernetzt. Während ein Prozessor die Tiefe überwacht, kann ein anderer den Antrieb regeln und das Drehmoment überwachen. Ein Weiterer übernimmt die Anzeige und die Bedienung. Da der Antrieb seinen eigenen Prozessor hat, ist er so schnell, dass er das Drehmoment ständig messen und bei einer Drehmomentüberschreitung in den Regelkreislauf eingreifen kann. Dies schützt Werkzeug und Werkstück vor Bruch und Beschädigung.
Qualitätsauswertung
Die intelligente Steuerung der Tauro und Taurox-Produkte macht eine prozesssichere Bearbeitung und Qualitätsauswertung möglich. So erfolgt die Überwachung der Parameter schon während der Bearbeitung. Bei der Qualitätsauswertung meldet der Monitor sofort die erzielten Ergebnisse, wie etwa fehlerfreie Bearbeitung, Grundberührung, Drehmomentüberschreitung, Werkzeugverschleiß, zu kleine oder zu große Bohrung.
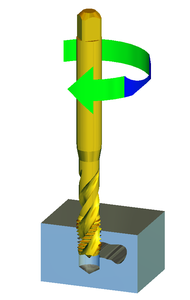
Erkennung von Lunker
(Lufteinschlüsse und Hohlräume)
in Gussteilen
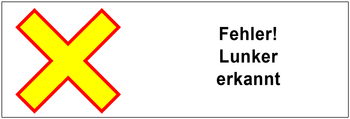
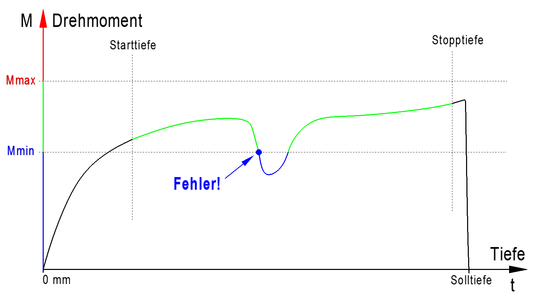
Dynamischer Antrieb
Der Synchron-Servomotor der Tauro und Taurox-Gewindebearbeitungsmaschinen mit aufwendiger Regelungstechnik erzielt eine sehr große Dynamik bei extrem gleichmäßigem Lauf im niedrigen sowie im hohen Drehzahlbereich. Daher ist selbst der Einsatz von Hartmetallwerkzeugen möglich.
Wissenswertes
Aus heutiger Sicht ist es sinnvoll, Gewinde durch Vorgaben der Qualitätssicherung und Kostendruck optimiert spanend (Gewindeschneiden) oder spanlos (umformend) Gewinde zu produzieren. Für die Gewindefertigung empfiehlt es sich dafür konzipierte Gewindefertigungseinheiten oder Gewindeschneidmaschinen zu benutzen. Diese sollen für eine prozesssichere Bearbeitung und Qualitätsauswertung sorgen.
Das Gewindeschneiden von Innengewinde, auch als Gewindebohren bezeichnet gehört als spanende Bearbeitung zum Fertigungsverfahren Trennen. In der Serienfertigung und Maschinenfertigung benutzt man so genannte Gewindewerkzeuge, den Maschinengewindebohrer (Einschnittgewindebohrer). Diese werden wieder in Durchgangsgewinde und Grundgewinde unterschieden. Bei der Bearbeitung von Durchgangslöchern ist die Schneidengeometrie des Gewindebohrers so ausgebildet, dass die Späne in Schneidrichtung aus dem Loch führen. Bei der Bearbeitung von Grundlöchern ist die Schneidengeometrie des Gewindebohrers so ausgebildet, dass die Späne entgegen der Schneidrichtung aus dem Loch führen. Dabei werden Maschinengewindebohrer mit Spiralnuten benötigt
Das Gewindeformen von Innengewinde gehört als spanlose Bearbeitung zum Fertigungsverfahren Umformen. In der Serienfertigung von mittleren Losgrößen bis hin zu großen Losgrößen und bei der Einbindung von Automationslösungen wird das Gewindeformen gegenüber dem Gewindeschneiden bevorzugt, da keine Späne anfallen, die Standzeit höher ist als beim Gewindebohrer, die Bearbeitungszeit durch höhere Schnittgeschwindigkeiten niedriger, die Materialoberfläche der Gewindeflanke glatter und das Material verdichtet und somit belastbarer ist. Zwischen der Bearbeitung von Grundgewinde und Durchgangsgewinde wird beim Gewindeformen nicht unterschieden. Der Schaft des Werkzeuges besitzt keine Spannuten.
Die höheren Taktraten erfordern höchste Ansprüche an das Gewindewerkzeug, Kühlschmierstoff, an Maschine und an den Menschen.
Da die Kühlschmierstoffe (umgangssprachlich Schmiermittel) sehr hochwertig und meist mit Additiven angereichert sind, sollte sparsam, aber ausreichend auf die Bearbeitungsstelle aufgebracht werden. Es haben sich für derartige Anwendungen Minimalmengenkühlmittelschmiersysteme bewährt. Diese sorgen für eine Minimalmengenkühlschmierung durch eine Dosier – Kolbenpumpe. Diese spritzt eine dosierte (einstellbare) Menge Kühlschmierstoff im micro – Liter (µl) in eine vorbeiströmende Blasluft. Somit entsteht ein Luft-/Ölgemisch. Dieses Prinzip eignet sich im Gegensatz zum Venturi-Prinzip auch für Flüssigkeiten mit höherer Viskosität. Der Luftstrom muss auch nicht so stark sein, da die Luft nur ein Träger des Kühlschmierstoffes ist. Dadurch entsteht kein Sprühnebel, der eine erhöhte Immissionskonzentration verursacht.
Die Maschine (Gewindemaschine) ist für die prozesssichere Bearbeitung ein wichtiger Faktor. Die Gewindeschneidmaschine amortisieren sich schnell, wenn man die Einsparung von Gewindewerkzeugen und Werkstückausschuss berücksichtigt. Durch eine elektronische Überwachung des Drehmomentes (Drehmomentüberwacht) während des Bearbeitungsvorganges und eine moderne Regelungstechnik lässt sich die Bearbeitungskraft feststellen. Die Drehmomentüberwachung (Drehmomentkontrolle) kann somit indirekt eine erhöhte Torsion, Werkzeugverschleiß / Standzeitüberschreitung und Grundberührung des Gewindewerkzeuges feststellen und rechtzeitig ein Brechen des Werkzeuges (Werkzeugbruch und Werkstückausschuss) vermeiden (Bruchschutz). Zusätzlich ist es möglich es möglich durch Veränderung der Schnittgeschwindigkeit (Drehzahl), Schmiermittel, Werkzeuggeometrie, Werkzeugbeschichtung richtig auszuwählen und zu optimieren. Dieses Verfahren bewirkt eine Optimierung des Prozessablaufes. Durch eine ständige Überwachung der Schnittdaten kann eine Aufwändige Prüfung von lehrenhaltigen Gewinden mit Grenzlehrdornen vermieden werden. Da das ideale Drehmoment ein Indiz für das optimale Bearbeitungsergebnis und die richtige Gewindetoleranz ist, kann somit ein Qualitätsauswertung und eine Gut-/ Schlechtselektierung bereits während der Bearbeitung vorgenommen werden. Zusätzliche aufwändige Qualitätskontrollen können somit eingespart werden.